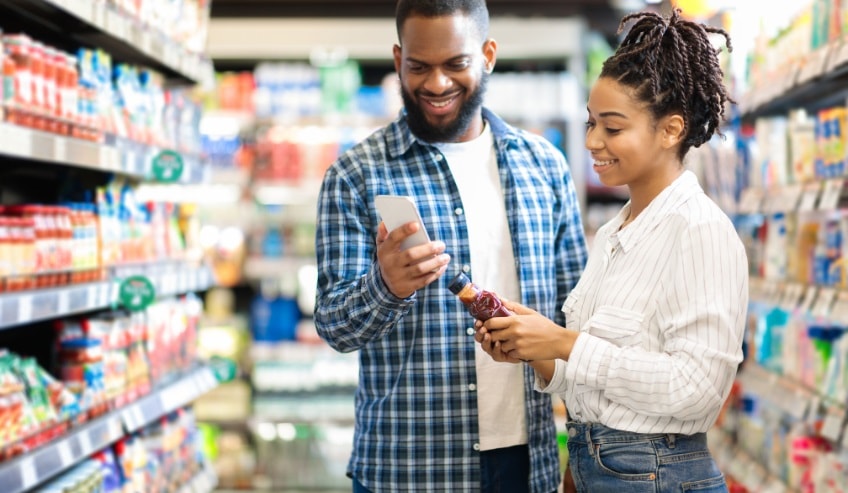
The Glue Talk Blog
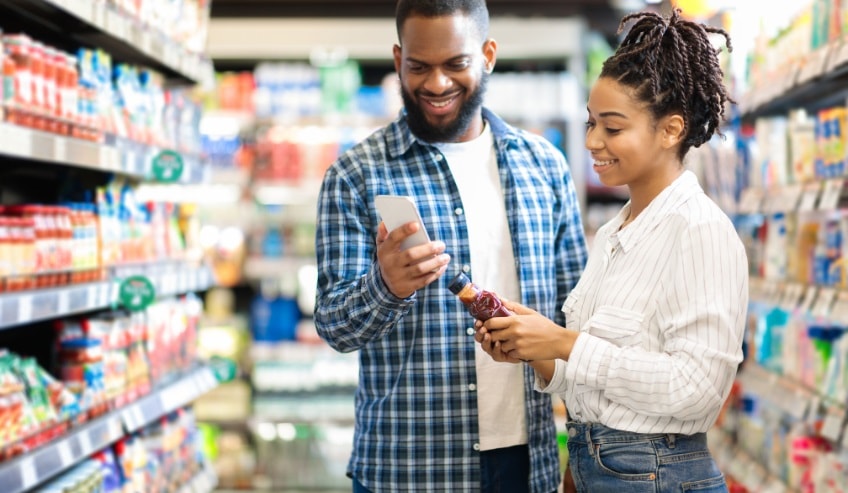
Have you ever picked up a stand-up pouch with a fuzzy logo or with graphics that were off the mark? If so, you have likely encountered ink smear, a scourge for brand owners and converters alike.
Brand graphics have an important story to tell in today’s competitive landscape, especially when making sustainability claims, such as recyclability or compostability. Anything that is not clear and unblemished risks being ignored or labeled as low quality in the marketplace.
According to Grocery Drive, consumers are moving toward either end of the price spectrum, with an increase at the cost-conscious and premium ends of the packaging market. For premium customers in particular, clear branding and messaging are key to the brand experience.
Understanding Ink Smear
When creating a positive brand experience, it is important to ensure your graphics and logo are unblemished and free of ink smear.
In the context of laminating, ink smear is the degradation of print quality, due to the movement of ink. This can range from fuzzy edges to inks bleeding into each other, and it is primarily caused by an incompatibility with either the chemistry of the inks and adhesives or the laminating process. Ink smear is typically associated with solventless adhesives, which can solvate the ink and cause smear or bleeding.
If it is chemistry-related, it is due to interactions or incompatibility between the adhesive and the ink. If the ink is softened or solubilized by the adhesive, it will flow and change the appearance of the printed image. An ink that is not completely dried or has excessive adhesive amounts can also contribute to ink smearing. Ensure inks are completely dry by running testing on the printed webs and suspend rolls during curing. Testing for ink smear should be performed when inks or adhesives are changed.
Ink smear primarily occurs during the lamination stage. Since this process happens towards the end of processing, if not controlled properly, it can contribute to a costly defect that has to be scrapped.
Ink and the Flexible Packaging Market
Ink has increasingly become more established in the flexible packaging market. When color systems were limited, a small amount of quality defects was deemed acceptable, though not ideal. Today, with multi-part and multi-color ink systems and more complex graphics, even the slightest imperfection can be quite noticeable and is unacceptable from a brand integrity standpoint. Large converters have begun to tweak or reformulate inks on-the-spot or work closely with their ink suppliers to ensure the best fit. Within the flexible packaging market, processes, chemistry, color, and the type of adhesive used can mean the difference between a superior package and one with quality concerns.
H.B. Fuller Can Help
Flextra® WD4120 / XR1550 is a universal two-part solventless adhesive system formulated for improved food packaging designs. H.B. Fuller engineers created this system for converters who have struggled with ink and adhesion interactions and are looking for reduced waste and minimal defects. It provides excellent machinability, pot life, and green bonds.
Our technical service team can recommend process changes to help eliminate ink smear, such as longer or hotter dry times and ink compatibility or other machine setting changes. At H.B. Fuller’s Center of Excellence, we can test your substrate with advanced analytics to give you the adhesive that suits your unique processing needs.
Blog Categories
Blog Categories
Archive
- 2024
- 2023
-
2022
- February (4)
- March (3)
- April (1)
- May (2)
- June (5)
-
August (6)
- Beverage Labeling Market In Africa: A Huge Potenial
- H.B. Fuller’s Glue House: Scavenger Hunt
- Increasing Global Aging Population: Impacts and Challenges
- Innovations and Key Challenges in Sustainable Disposable Absorbent Hygiene Products
- Supporting Racial Equity in Our Community
- Top 5 Reasons to Invest in H.B. Fuller
- September (4)
- November (2)
- December (2)
-
2021
- January (3)
-
February (7)
- Celebrating Exceptional Service During COVID-19 Complications
- Cyanoacrylates: What They Are and What They Do
- Innovative two-shot bookbinding adhesive
- Make a Difference 2020
- Problem Solving: Paper straws in drinking beverages
- Stronger straws
- Substances of Interest in Disposable Absorbent Hygiene Products
- March (4)
- April (4)
- May (4)
- June (5)
- July (2)
- August (5)
- September (2)
- October (1)
- November (3)
- December (2)
-
2020
- January (4)
- February (2)
- March (3)
- April (4)
- May (3)
-
June (7)
- Community Support in the Era of Coronavirus
- Employee Creates Face Shields with 3D Printer
- Improved Packaging Integrity and Greater Customer Satisfaction
- Liquid-Resistant Paper Straws
- What is a Sealant
- What Is the Future of Commercial Disinfectants
- Winning over consumers with e-commerce packaging solutions
-
July (6)
- Employees Take Action to be Part of Healing and Growth
- Gain a competitive advantage with packaging adhesive solutions
- HB Fuller Company Foundations Commitment to Communities
- Packaging Solutions for the South African Agriculture Market
- Supporting Organizations That Provide STEM Education for Youth
- Where Does Sustainability Stand Amid COVID-19
- August (3)
- September (2)
- October (4)
- November (2)
- December (4)